What is the auger filling machine working principle? Generally, it includes a feed hopper, a feed pipe, a pump, and a discharge pipe. The feeding pipe and the pump are connected to the upper part of the feeding hopper, and a stirring shaft connected to the pump is installed inside the feeding hopper. A solenoid valve is installed at the outlet end of the feed hopper, and the solenoid valve is connected with the discharge pipe to ensure that the material packaging is carried out in a continuous environment. Adjust the number of revolutions of the auger to control the filling volume. Replacing different screws can achieve 50g-5000g packaging.
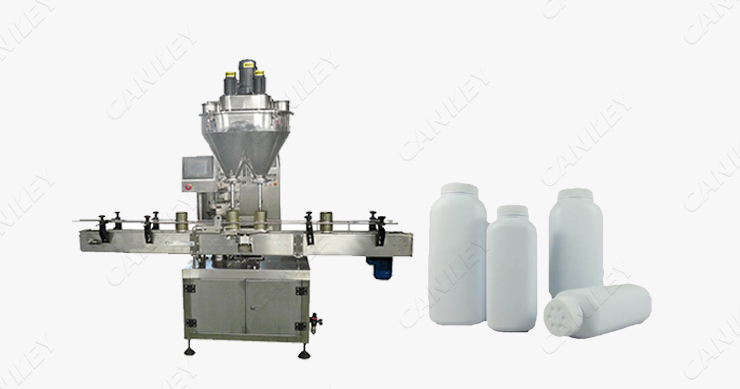
Features:
- Versatile, filling a wide variety of free-flowing or non-free-flowing powders into a variety of containers.
- User-friendly control panel, easy to operate, can store formulas with various parameters, and can realize one-key switching of packaging specification changes.
- Servo screw drive with separate agitator and servo motor.
- Using a fully sealed glass and stainless steel combination material box, the condition of the material is clear at a glance, and the dust does not leak.
- Integrated fault lights and alarms to notify operators of production errors.
- All material contact parts are made of 304 stainless steel, in line with GMP/food hygiene and other relevant certification requirements.
- Adjustable conveyor rails accommodate different types of bottles.
- Fully interlocked protection to ensure the safety of the filling area.
- Stable work, anti-interference, high weighing accuracy, weighing feedback type specific gravity tracking, overcomes the shortcomings of packaging weight changes caused by material specific gravity changes.
The auger filling machine working principle is very simple, and the operation process is also very simple, which can effectively help manufacturers to automate the packaging process.